Lithography is the process of transferring circuit pattern directly on to the
silicon wafer. But first, the designer must have designed the circuit, determined
the size of various circuit elements down to transistor bases to lead width, and
their exact positions on the chip. All of the layout information is converted into
computer data files that can be used either by a photolithography system or an
electron-beam lithography (EBL) system (See Figure 2).
Working from a circuit diagram, a set of individual photomasks (Figure 3) is needed
to define buried layers, contact windows, resistors, and so on. An integrated circuit
typically requires a mask for each structurally defined step in fabrication. The
process of mask making starts with a square glass plate that is little larger
than the slice to be printed. It is then coated with chromium, an opaque metal
in the wavelength region used to expose resist. Extreme care is taken to make
sure that there are no pinholes or dust particles in the metal coating because
they will remain as part of the finished mask. The metal is then coated again
with a layer of electron-sensitive resist for EBL systems, or photosensitive resist
for photolithography systems. Patterns are created on this resist layer either by
turning on or off the electron beam about the surface, or exposing it to the
appropriate image.
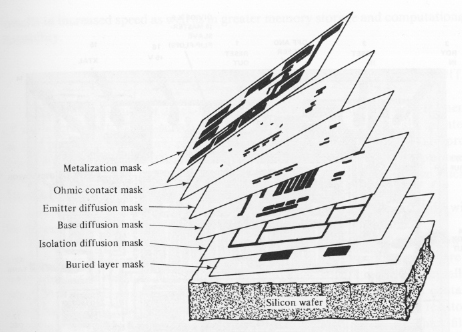
Figure 2: Series of photo masks.
The light used in EBL is very intense so that exposure can be quite short. Since
a typical mask can be few inches in square, and since electron beams can be
deflected over only a small angle without distortion, a complete mask is made by
repeating a given design until the entire mask is exposed. Electron beam exposure
is rather slow because of its low energy and relatively insensitive resist. But
because the diffraction effects of electrons are much less than that of lights
in photolithography, EBL is the preferred method when high-resolution masks are
desired. Advantages of EBL process include smaller line - width, thus producing
high-quality masks, and provide simple modification process by altering the computer
data file containing the design.
Before resist can be exposed, mask alignment must be carefully checked and
rechecked to avoid circuit defects. The accuracy of alignment generally includes
marker matching between levels. The three basic types of mask aligners are
contact, off-contact, and projection printing. In contact alignment, the mask is
placed directly on top of the wafer and it is either aligned manually or
automatically. Then the wafer is vacuum clamped tightly with the mask. After
rechecking alignment and it is found to be satisfactory, resist exposure is carried
out. In off-contact alignment, there is a 5 to 30 um separations between wafer
and mask. The lack of contact reduces the wear on the mask but at the same time
making accuracy more difficult to achieve. Due to possible warping of wafer, great
care must be taken to ensure the wafer is flatten and that the wafer is almost
perfectly paralleled to the mask. In the projection printing approach of mask
alignment, an image of the mask is literally projected onto the wafer using either
transmitting or reflecting optics. Its performance is similar to off-contact
alignment concerning mask wear. In the case where transmitting optics are used,
the process must use monochromatic light source to minimize chromatic aberration.
In doing so, it requires a longer exposure time and is also subject to the negative
effects of interference layers in negative photoresists. The interference layer
is the result of either constructive or destructive interference of light when
it is reflected from the top of the oxide and silicon surface. Constructive
interference occurs if the path-length difference is a multiple of the wavelength,
whereas destructive interference occurs at odd integral multiple of the half-
wavelength. The phenomenon reduces edge definition since during the rinsing process,
some of the unexposed resist will tend to be removed. On the other hand, the
reflective optical process can avoid the problem of chromatic aberration.
The first resists used in semiconductor fabrication process were of negative type
in which negative images were produced. Solvents can remove resist layers unless
they are exposed to ultraviolet light. In the fabrication of large-scale integrated
circuits, use of positive resists is preferred over negative resists. The positive
resists have shorter polymer links and therefore easier for the solvent to break
up. A higher resolution of the circuit design is achieved with a thinner resist
layer. But the draw back is its higher density of pinholes. Therefore, the modern
lithography process usually employs two layers of resists for design exposure.
Positive resists are also in use later on. A different chemical based solvent is
used to remove regions that have been exposed to light, rather than regions that
have not been exposed.
The two different types of resists that you would mostly likely encounter in
fabrication are photoresists and electron resists. Traditionally, the contact
alignment process is used to achieve a small line width of 2 um within the tolerated
diffraction around the edges of mask patterns. As mentioned earlier, direct contact
causes damage to the wafer and mask. The development of laser interferometry was
able to improve the tolerance by using projection printing.